Industrial materials
Hygro-master (Industrial air dryer)
Importance of the compressed air at the production site
Currently the compressed air has being used as high-reliable energy with the affordable and safe facilities for Factory Automation at the production site.
For power source
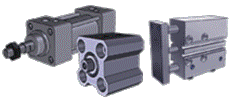
・Automatic control of equipment
・Automatic transportation of products
For coating
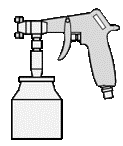
・Splay
For drying/cleaning
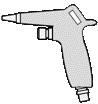
・Drying
・Blowing away foreign substances
The problem in use the compressed air is draining. The condition the drain is in the gas causes below troubles.
Drain is a great enemy for machines
・failure and breakdown due to rusting in the device
・powder solidification and clogging during the transportation
・coating failure such as unevenness and cissing
・failure due to water mark (desiccation crack) at drying process
Dehumidification is necessity for long-life devices and product high-quality
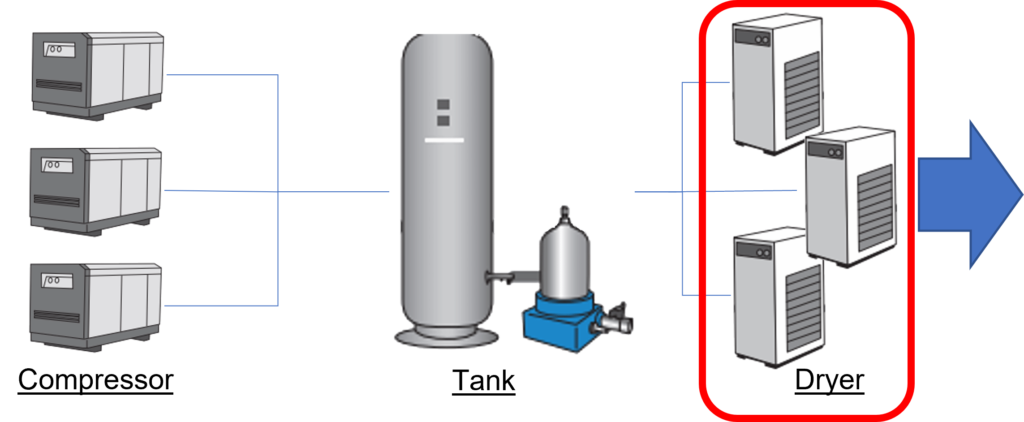
Importance of big energy for dehumidification
The utility related to the air pressure including the air compressor is 30% of the entire factory. It means the energy-saving dehumidification device (drying machine) is necessity.
Industrial air-conditioner
4 units (1.5HP*4)
Cooling type dehumidifying device
for general factories
1 unit (5.6HP)
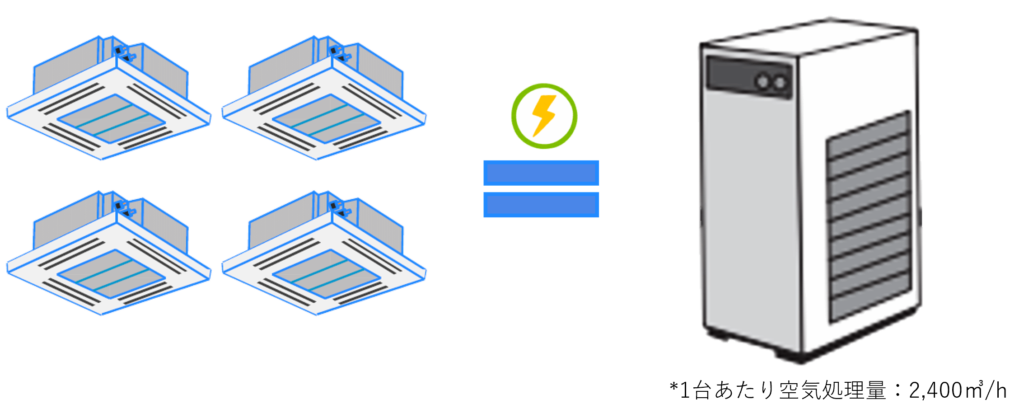
Actually, in most of large factories, the compressed air which is over 50,000㎥/h have been used, so many dehumidifying devices are needed for that situation.
In general, the energy-saving is executed by adopting inverter and unit control but the dehumidification is still untouched by companies.
By solving this matter, it is possible to get a big lead from other companies.
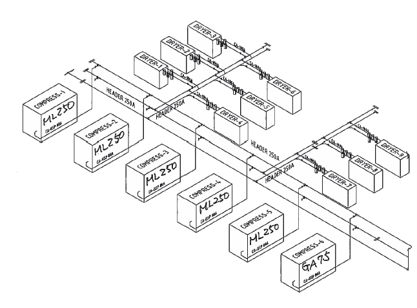
Energy-savingdehumidifying device
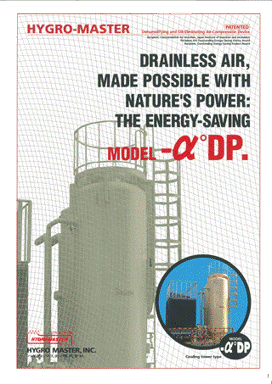
New concept dryer
By using our recommend Hygromaster’s dryer, it is possible to save cost dramatically from the standpoint of the power cost and the pressure loss more than using the general cooling type dehumidifying device.
Cost-saving of up to 73%
Saving of operation(Energy-saving)
Types | HYGRO-MASTER -・DP(AE)-10000 | Conventional freezer |
Air processing capacity | 10000m3/H | ← |
Air pressure | 0.6MPa | ← |
Temperature of inlet air | 42℃ | ← |
Dew point of outlet air(under pressure) | Summer 30℃ Winter 10℃ (Temperature set lower automatically than the open air) | 10℃ |
Power breakdown | Cooling tower(100RT) 2.2kW Circulation pump(1000L/min) 5.5kW | Cooler 20kW Cooling water C/T(20RT) 0.4kW Pump (260L/min) 1.5kW |
Total power | 7.7kW | 21.9kW |
Annual operation time | 3840 hours (16 hours×20 days ×12 months) | ← |
Cost per 1kW/H | 14 Yen | ← |
Total cost | ¥413,952- | ¥1,177,344- |
Comparison | 35.10% | 100% |
Pressure loss in the device becomes low (energy-saving)
Types | HYGRO-MASTER -・DP(AE)-10000 | Conventional freezer |
Air processing capacity | 10000m3/H | ← |
Air pressure | 0.6MPa | ← |
Power loss breakdown | Device 0.015MPa | Device 0.015MPa Line filter 1 0.038MPa(0.005~0.07MPa) Line filter 2 0.038MPa(0.005~0.07MPa) |
Total power loss | 0.015MPa | 0.096MPa |
Operation loss by power loss | 0.015MPa loss meets with 1.3% compressor loss. | 0.015MPa loss meets with 8.7% compressor loss |
Compressor power | 1000kW(1kW=10m3/H) | ← |
Annual operation time | 3840 hours (16 hours×20 days×12 months) | ← |
Cost per 1kW/H | 14 Yen | ← |
Total cost of loss | ¥698,880- | ¥4,677,120- |
Comparison | 14.90% | 100% |